Idea P-FMEA
Przygotowując proces produkcji danego produktu lub grupy produktów, dążymy do jego zoptymalizowania pod kątem wydajności oraz minimalizacji występowania wad. W trakcie realizacji procesu, gdy pojawiają się problemy z jakością, podejmujemy działania mające na celu poprawę tego procesu. Po pewnym czasie udaje nam się zidentyfikować większość problemów, co pozwala osiągnąć stabilność procesu i wysoką jakość produktów.
Należy jednak podkreślić, że taka metoda pracy jest kosztowna, ponieważ na początku procesu produkcji często pojawia się dużo wad, a dopiero po jego dopracowaniu ilość tych wad maleje. Ponadto, takie podejście może wpływać negatywnie na nasze relacje biznesowe, co jest niewskazane. W praktyce przypomina to bardziej podejście typu "metoda prób i błędów" lub "rozpoznanie bojem", co niesie ze sobą niepotrzebne koszty.
Jednak istnieje metoda, która pozwala przewidzieć większość potencjalnych wad produktów oraz ich źródeł w procesie produkcji, a następnie zmniejszyć te problemy do minimum przed uruchomieniem produkcji seryjnej. Mowa tu o analizie rodzajów błędów i ich skutków w procesie, znanej jako P-FMEA (ang. Process Failure Mode and Effects Analysis).
W ramach tej metody proces produkcji jest podzielony na mniejsze, bardziej zarządzalne "kroki procesu", dla których przeprowadza się odpowiednie analizy.
Czy P-FMEA działa?
Poprawne zastosowanie P-FMEA ułatwia wdrożenie wyrobu do produkcji, przez co zwiększa szanse na sukces firmy. Dzięki P-FMEA możemy zauważyć znaczące ryzyko i je zredukować, zanim uruchomimy produkcję seryjną. Możemy ograniczyć poziom napraw i złomowania oraz poprawić wydajność, czyli finalnie obniżyć koszty.
Warto skupić się na odpowiednim wykorzystaniu - to znaczy, gdy dokonamy analizy w odpowiednim czasie (co jest kluczowe) i podejdziemy do niej w odpowiedni sposób (równie ważne). Analiza powinna być przeprowadzona w celu zrozumienia naszych własnych potrzeb, a nie tylko dla klienta czy audytora. W efekcie uzyskamy przegląd procesu, wskazujący na konkretne niedoskonałości, ich źródła oraz sugestie dotyczące jego usprawnienia. Poprzez wdrożenie odpowiednich działań zmniejszających ryzyko, jesteśmy w stanie ograniczyć potencjalne straty.
Kluczowym aspektem jest "poprawne zastosowanie" - czyli jeżeli wykonamy analizę w odpowiednim czasie (bardzo ważne), z odpowiednim podejściem (także bardzo ważne), wykonamy ją "dla nas" a nie "dla klienta/audytora", to wtedy otrzymamy pewnego rodzaju przegląd procesu z określonymi wadami, przyczynami wad i pomysłami na poprawę procesu. Jeżeli na tej podstawie wdrożymy jakieś sensowne działania redukujące ryzyko, to ograniczymy potencjalne straty.
Sensowne działania to techniczne rozwiązania redukujące występowanie przyczyn lub wykrywające przyczyny czy też wady. Przykładowe działania to eliminacja zbędnych czynności (np. transportów), automatyzacja procesów, error-proofing / mistake-proofing, zwiększenie zdolności procesów, doskonalenie technicznych metod detekcji.
Działania mało sensowne to zwiększenie częstotliwości inspekcji, dodatkowa inspekcja, kolejne przeszkolenie już wielokrotnie przeszkolonego operatora ;) i inne pomysły na "zwiększenia czujności operatorów"..
Kto realizuje P-FMEA?
P-FMEA to idealne narzędzie dla osób, które odpowiadają za wdrożenie produktu do produkcji.
Kiedy uruchomić P-FMEA?
P-FMEA staramy się uruchomić jak najwcześniej, najlepiej na początku wdrożenia wyrobu do produkcji przed zamówieniem narzędzi lub specyficznych maszyn.
Rola kierownictwa
Zaangażowanie kierownictwa ma kluczowe znaczenie dla sukcesu P-FMEA w zakładzie. Kierownictwo powinno zapewnić zasoby oraz określić, kto odpowiada za nadzór nad P-FMEA, nadzorować wdrożenie działań doskonalących itd. Nie należy przenosić tej odpowiedzialności na dział jakości lub na konsulatów.
Etapy P-FMEA
W zależności od przyjętego standardu, istnieją pewne różnice w przeprowadzaniu analizy P-FMEA, jednak ogólnie można wskazać kilka kluczowych kroków w jej realizacji:
- Ustalenie zespołu realizującego P-FMEA.
- Zdefiniowanie zakresu analizy.
- Określenie kroków procesu.
- Określenie funkcji oraz wymagań (tzw. analiza funkcji).
- Identyfikacja wad, skutków tych wad oraz przyczyn wad (tzw. analiza błędów).
- Określenie metod prewencyjnych i detekcyjnych, wskaźniki: S, O, D, RPN/AP (tzw. analiza ryzyka).
- Ustalenie działań redukujących ryzyko i ich wdrożenie.
- Ponowna ocena ryzyka (po wprowadzeniu działań).
- Identyfikacja charakterystyk specjalnych oraz zapewnienie poprawnego nadzoru.
- Opracowanie dokumentu plan kontroli i powiązanie go z P-FMEA.
- Aktualizacja P-FMEA pod wpływem danych z procesu, z reklamacji, w ramach 8D lub Global 8D.
Poniższy przykład to część analizy, gdzie ujęto relację między krokiem procesu - funkcją - wadą - skutkiem wady oraz przyczyną wady.
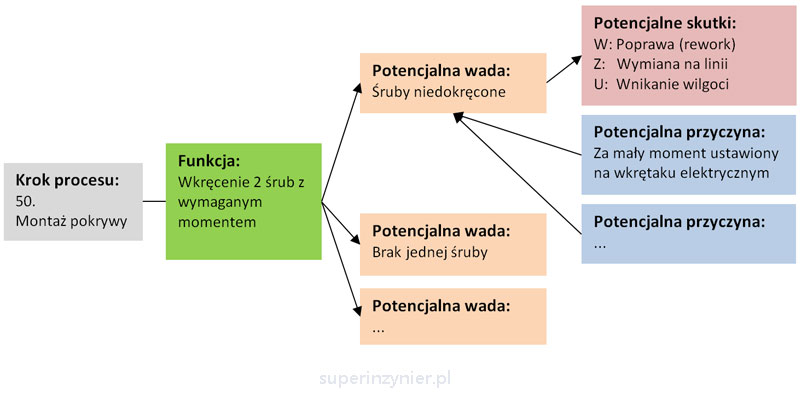
Standardy P-FMEA
Istnieje wiele standardów związanych z realizacją P-FMEA. Poniżej kilka z nich:
- AIAG FMEA
- VDA FMEA
- AIAG-VDA FMEA
- SAE J1739
- Specyficzne metody niektórych producentów pojazdów (OEM): Ford, PSA, Renault itd.
- AS-13004 (lotnictwo).
- Inne.
Jeśli mamy swobodny wybór standardu, osobiście preferuję AIAG FMEA-4 (choć jest to starsza wersja) lub bardzo dobrze opracowany SAE J1739:2021 (najnowsza edycja, powiązana z AIAG-VDA FMEA). Te metody można stosunkowo łatwo wdrożyć bez konieczności zakupu specjalistycznego oprogramowania, a przy odpowiedniej implementacji mogą przynosić znakomite rezultaty.
Metoda AIAG-VDA FMEA, która obecnie (w 2023 roku) jest wymagana przez większość producentów OEM w branży samochodowej, również może być używana. Jednak dla bardziej skomplikowanych procesów, może być trudno ją efektywnie zastosować w arkuszu kalkulacyjnym. W takich przypadkach warto rozważyć użycie specjalistycznego oprogramowania.
AIAG-VDA FMEA posiada także pewne subtelności, które mogą wpłynąć na mniej efektywne rezultaty.., ale to temat na inny artykuł ;)
Zapraszam do zapoznania się z krótkim artykułem: Historia FMEA.
Więcej informacji o różnych wariantach analizy FMEA przeczytasz w artykule: Rodzaje FMEA.
Podsumowanie
P-FMEA to świetna metoda przewidywania potencjalnych strat w procesie produkcji przed ich wystąpieniem. Odpowiednio użyta analiza pozwala na redukcję potencjalnych kosztów i zwiększa szanse na sukces danego projektu. Dlatego poprawne stosowanie P-FMEA powinno być aspektem o dużym znaczeniu dla kierownictwa firmy.